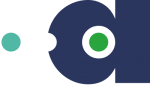
Sterilization of single-use medical devices
Aurora plasma is a solution for sterilizing single-use medical devices, in small and large packaging.
It solves the difficulties faced by manufacturers whose innovations are not compatible with existing technologies.
Plasma : the new sterilization for new medical devices
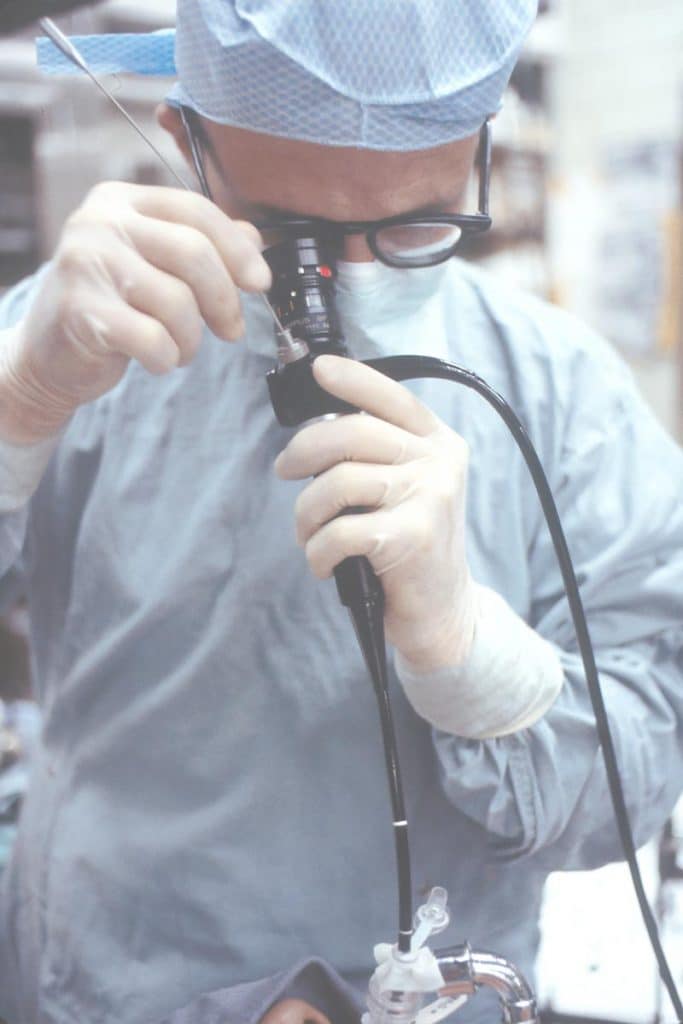
When a manufacturer develops a new medical device, he sometimes neglects sterilization.
He invests a lot of resources in his innovation. And suddenly he realizes that his device is difficult or impossible to sterilize with existing technologies.
In the best of cases, he operates a reconfiguration of his invention.
In the worst case, he must abandon his project.
In both cases he wasted time and money.
The greatest price for this neglect is paid for patients : they lose the chance to benefit from an innovation that would have improved their health.
Aurora plasma is compatible with many innovations in the medical device. It operates at low temperature between 30 and 40°C. It does not leave toxic residues. It penetrates complex shapes. It does not damage fragile materials.
As such, Aurora plasma has been recognized by several manufacturersfor sterilizing their innovative single-use medical devices.
Aurora plasma is particularly suitable for example for biodegradable polymers, silicone, foams, electronic components or cellulose.
Difficulties in increasing industrial sterilization capacities industrial sterilization
Another reason for developing a new sterilization technology is on the side of industrial sterilization players.
These are manufacturers who sterilize medical devices in their factories on behalf of manufacturers.
Sterilization at the end of the production line represents only a quarter of the volumes of the industry. Everything else is outsourced. Indeed, below 1 million € of sterilization costs, it is considered that it is better to entrust this phase of production to a specialist partner.
These contracted sterilization specialists face challenges in increasing their capacity.
Indeed, market growth has reached 7% per year in recent years. However, sterilization manufacturers are unable to keep up with the demand from manufacturers.
To understand why capacities are not increasing, it is necessary to know the constraints posed by existing sterilization technologies.
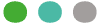
Strong political constraints on gamma rays and ethylene oxide
Leaving aside high temperature sterilization, there are two main cold sterilization techniques: gamma ray irradiation (Cobalt 60) and ethylene oxide vapor (EtO).
These two techniques share approximately equally a global market of $3 billion.
X-rays, beta rays (or electron gun) are other methods of cold sterilization by irradiation, but their uses are limited. They will not be discussed here.
Gamma irradiation and EtO are effective sterilizing agents but dangerous to the environment and human health. They must be implemented in industrial installations with high safety guarantees.
Government authorities have tightened security conditions for 20 years. It is therefore not easy to open new capacities.
For example, the last gamma-ray treatment site created in Europe could only be created because it was located on a former nuclear research site. The project took 10 years to complete.
In addition, the production of the gamma irradiation source (cobalt 60) is threatened. The cobalt requirements of electric vehicles make this metal more difficult to obtain. And there are very few nuclear reactors capable of producing the desired isotope. Capacity growth is therefore very constrained on this side.
As for ethylene oxide, the American and European authorities issued alerts in 2019 and 2020 on its use for industrial sterilization. Abnormally high emissions around facilities inIllinois and Georgia led to their shutdowns in 2019. Their presence even became an election issue. In France, a recent accident has highlighted the risks posed by this sterilizing agent on the environment and the health of local residents.
At the end of 2020 the European Chemicals Agency issued an opinion on the use of ethylene oxide in sterilization. It confirms that there is no monitoring system for ethylene oxide emissions in the vicinity of sterilization plants in Europe. That the dangers posed by this chemical compound would justify its ban. But that until then there was no technically and financially viable solution to replace it. Therefore the Agency allowed the use of ethylene oxide for the sterilization of medical devices as long as no substitute was found.
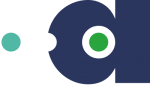
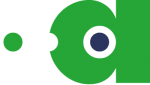
The advantages of Aurora plasma for sterilizing large volumes
The advantages of plasma for the reprocessing of reusable medical devices in the hospital are the same as for single-use devices:
- Low temperature: between 30 and 40°C
- Respect for fragile materials
- Penetration of complex shapes
- Process safe for human health and the environment
- Moderate operating costs
Aurora develops a sterilizer capable of processing one or several pallets of medical devices at the same time.